МЕТАЛЛЫ ЧЕРНЫЕ - железо и его сплавы, важнейшие конструкционные материалы в технике и промышленном производстве. Из сплавов железа с углеродом, называемых сталями, изготавливаются почти все конструкции в машиностроении и тяжелой промышленности. Легковые, грузовые автомобили, станки, железные дороги, корпуса и силовые установки судов - все это делается в основном из стали. Масштаб производства стали является одной из основных характеристик общего технико-экономического уровня развития государства. На долю стали приходится около 95% всей металлической продукции. Важная роль железа и его сплавов в технике и промышленности обусловлена удачным сочетанием их свойств и ряда других факторов. Во-первых, в земной коре очень много железной руды; ее залежи встречаются повсюду, а добыча не представляет особых трудностей. Во-вторых, из железной руды довольно легко выплавляется железо. Благодаря обилию руды и относительной несложности выплавки железо - недорогой и широко распространенный материал. В-третьих, на основе железа можно получать широкий спектр конструкционных материалов разного рода, обладающих самыми разнообразными свойствами. Например, чугун - прочный материал с довольно низкой температурой плавления, которому путем литья можно придать любую форму. Сталь, в зависимости от ее состава, может быть либо прочным, но пластичным материалом для изготовления, скажем, профильного проката, из которого строят мосты и морские суда, либо очень твердым и тугоплавким материалом для металлорежущего инструмента. В-четвертых, железо - единственный известный недорогой магнитный материал, а потому из него можно делать магнитные сердечники трансформаторов, электромашинных генераторов тока и электродвигателей.
Сплавы железа. Чистое железо в технике почти не применяется. Одним из первых видов вырабатывавшегося железа было сварочное железо, практически чистое, но в настоящее время оно не находит заметного применения. Конструкционные материалы любого назначения с наиболее подходящими свойствами получают, сплавляя железо с другими химическими элементами.
Сталь - это, прежде всего, сплав железа с углеродом. В такой сплав могут входить и другие элементы, но углерод - непременный компонент стали. Содержание углерода в стали может достигать примерно 2%. В нелегированной стали другим компонентом может быть только марганец. Он вводится для снижения хрупкости, обусловленной присутствием в стали серы, которая не удаляется при промышленном переплаве. Содержанием углерода определяется прочность нелегированной стали. Сталь, содержащая ок. 0,2% углерода, называется конструкционной и пригодна для изготовления каркаса, скажем, высотного дома или автомобиля. С увеличением процента углерода сталь становится тверже. При 0,8% С сталь пригодна для изготовления сверл и молотков, при 1% - бритвенных лезвий и напильников. Такие "высокоуглеродистые" стали называются инструментальными. Для повышения ударной вязкости или для сохранения прочностных характеристик при повышенных температурах к стали могут добавляться и другие легирующие элементы (никель, хром, молибден, вольфрам, ванадий) общим количеством примерно до 5%. Такие стали называются легированными. В состав нержавеющих сталей входят хром и обычно никель в суммарном количестве до 25%. Нержавеющие стали прочны и антикоррозионны. К чугунам относятся сплавы железа с углеродом, содержащие более 2% углерода. Почти всегда в них входит и кремний. Углерод и кремний в значительном количестве понижают температуру плавления и повышают жидкотекучесть расплава. Чугун может выплавляться в простых, недорогих печах, а благодаря его высокой жидкотекучести - разливаться в литейные формы сложной конфигурации. Из чугуна изготавливают столь разнообразные изделия, как рояльные рамы, трубы и сковороды, а также станины прокатных станов, токарных и фрезерных станков. Железный сплав, содержащий 3-4% углерода и кремния, называется серым чугуном из-за цвета поверхности его излома. При меньшем содержании углерода и кремния и быстром охлаждении отливки получается твердый и хрупкий белый чугун. При литье в кокиль на части или на всей поверхности отливки образуется слой износостойкого белого чугуна. Отливки из белого чугуна можно термообработкой превратить в ковкий чугун, по механическим свойствам близкий к мягкой (малоуглеродистой) стали. Повышение пластичности чугуна обусловлено перераспределением углерода в металле при отжиге. Сходные результаты достигаются путем добавления в расплавленный чугун такого элемента, как никель; получающийся при этом материал называется чугуном с шаровидным графитом. Чугун можно разливать по изложницам непосредственно из доменной печи и обрабатывать, обходясь минимумом крупного оборудования. Когда промышленно развитые страны достигают высокого уровня благосостояния, они начинают больше средств инвестировать в сталеплавильное производство, а потребление чугуна снижается.
ПРОИЗВОДСТВО ЧУГУНА
Основной сектор черной металлургии - выплавка передельного чугуна в доменной печи. Для работы доменной печи необходимы большие количества руды, топлива (каменного угля), известняка и воды (для охлаждения). Железная руда и топливо в наши дни могут быть доставлены в любую точку мира. Поэтому, например, в Японии чугун может выплавляться из руды, добытой в Австралии, и на угле из Западной Виргинии (США).
Доменная печь. При достаточно высокой температуре оксид железа реагирует с моноксидом углерода (CO), давая диоксид углерода (CO2) и металлическое железо. Доменная (шахтная) печь устроена так, чтобы реакция могла протекать непрерывно. На практике сверху вниз по шахте печи непрерывно продвигаются углерод и оксид железа, а навстречу им снизу движется воздух. Углерод в виде кокса играет двоякую роль: при сгорании он нагревает печь и образует газ CO, который восстанавливает оксид железа до металла. В верхней части печи из нее отводится диоксид углерода, а в нижней - выпускается жидкий металл. Обычно печь работает непрерывно до ее остановки для ремонта внутренней кирпичной кладки (футеровки). Основные реакции, протекающие в доменной печи, можно представить простыми уравнениями. Когда вдуваемый воздух приходит в контакт с коксом, последний горит:

образуя газообразный моноксид углерода. Этот газ является основным восстановительным агентом для оксида железа. Восстановление протекает в три стадии
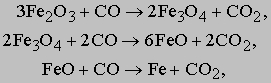
когда температура опускающейся смеси руды с коксом достигает 600-700° С. В результате образуется твердое, но пористое губчатое железо, которое затем плавится в нижней, более горячей части доменной печи (горне). Если бы доменную печь можно было загружать чистыми оксидом железа и углеродом и продувать чистым кислородом, то термохимия доменной печи сводилась бы к написанным выше простым уравнениям. На самом же деле во вдуваемом воздухе больше азота, чем кислорода, а руда может содержать свыше 50% безрудных минералов (пустой породы), в основном силикатов. Азот проходит через печь, не вступая в реакцию, но с силикатами дело сложнее. Чтобы можно было отделить силикаты от железа и вывести из печи, они должны быть жидкими. Силикаты, содержащиеся в железной руде, образуют расплавленный шлак при взаимодействии с известью CaO. Для этого в печь вместе с рудой загружают в нужной пропорции известняк CaCO3. Известняк, или "флюс", разлагается в верхней части печи соответственно реакции

образуя известь, необходимую для перевода силикатных примесей железной руды в жидкий шлак. Доменная печь дает почти столько же шлака, сколько и чугуна. Затвердевая, шлак превращается в темный стекловидный материал, который в прошлом накапливался в больших шлаковых отвалах возле передельных металлургических заводов. В наши дни шлак идет на изготовление заполнителя для бетона, железнодорожного балласта, шлаковаты и противоюзового покрытия автомобильных дорог. Из сказанного выше вытекают основные требования к конструкции доменной печи. Она должна обеспечивать непрерывную загрузку топливом, рудой и флюсом сверху, непрерывную подачу воздуха и периодический отвод жидких продуктов снизу. Печь должна быть достаточно высокой, чтобы успевали протекать необходимые химические реакции. Воздух вдувается в печь через фурмы, расположенные в ее нижней части, и поднимается сквозь шихту вверх. Восстановленное губчатое железо и шлак плавятся на уровне "заплечиков", в самой широкой части печи, а жидкость накапливается в горне, ниже фурм. В горне периодически пробивают заделанные глиной летку для выпуска металла и (несколько выше) шлаковую летку.
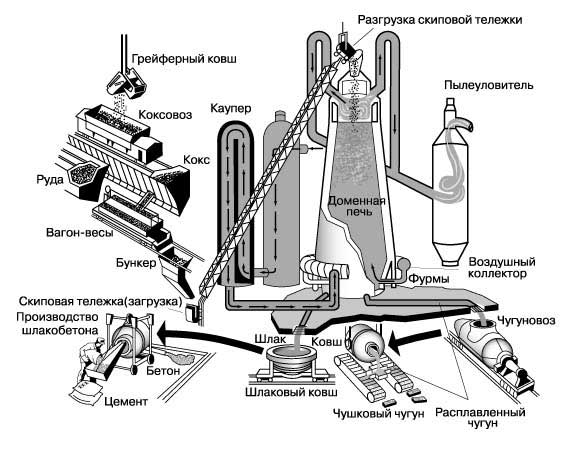
РАБОТА ДОМЕННОЙ ПЕЧИ. Дозируемые количества кокса, руды и известняка транспортируются в скиповых тележках на верх печи, где они разгружаются. В нижнюю часть печи непрерывно вдувается нагретый воздух. Шихта нагревается и медленно опускается в шахте печи. Кокс, превращаясь в газообразный моноксид углерода, отбирает кислород у руды (которая представляет собой оксид железа), в результате чего образуется пористое металлическое железо. Опустившись примерно на 2/3 высоты, металл плавится и стекает вниз. Известняк, вступая в реакцию с примесями в железе, образует расплавленный шлак - стеклоподобную жидкость, которая скапливается на поверхности расплавленного железа. Моноксид углерода, остающийся после неполного сгорания кокса, отводится по газоходу из верхней части печи, очищается от пыли и подается в воздухонагреватель (каупер), где сжигается для нагревания воздушного дутья. После вскрытия летки расплавленный чугун заливается в чугуновозы, из которых он может разливаться по изложницам для затвердевания в виде чушек или заливаться в кислородный конвертер с металлоломом и флюсом для передела в сталь. Расплавленный шлак выводится через шлаковую летку, а после затвердевания дробится, образуя материал для бетона и теплоизоляционных плит.
Восстановление оксида железа до губчатого железа и разложение известнякового флюса происходят в шахте - основной части доменной печи - в процессе медленного оседания шихты. Шихта начинает разогреваться в колошнике - верхнем конце шахты. Диоксид углерода и азот непрерывно отводятся по широкому газоходу из колошника. Поскольку при нормальной работе доменной печи давление газов в колошнике выше атмосферного, верхний конец печи нельзя просто открывать для загрузки, иначе упадет давление газов и из печи будут выдуваться наружу тонкоизмельченные компоненты шихты. Для предотвращения этого предусмотрен двухконусный шлюзовой засыпной аппарат. Нижний конус поднимают так, чтобы он газоплотно закрывал загрузочное отверстие, а затем опускают верхний для загрузки. После этого снова поднимают верхний конус, герметизируя вход в печь, и, опустив нижний, пропускают порцию шихты (колошу) в колошник. Современная доменная печь представляет собой крупное сооружение. Высота печи, производящей 1000 т чугуна в сутки, составляет около 30 м, а диаметр на уровне заплечиков - ок. 8 м. Печь устанавливается на бетонном фундаменте, на котором в стальном кожухе выводится кладка из огнеупорного кирпича. Нижняя часть этой конструкции охлаждается водой. Сколь ни внушительны размеры доменной печи, сама она - лишь малая часть чугуноплавильного завода. Для ее нормальной работы нужны еще отделение шихтовых материалов, грузоподъемные устройства для загрузки печи, насосы для подачи воздуха (дутья) и воздухонагреватели (кауперы), шлаковозы и литейный цех или приемная система для расплавленного металла. Для загрузки доменных печей иногда применяются ленточные конвейеры, но чаще руда, топливо и флюс подаются скиповыми подъемниками - небольшими сосудами (скипами), движущимися на колесах по наклонным рельсам от нижних засыпных бункеров до верхней загрузочной площадки, где они автоматически опрокидываются, разгружаясь в приемную воронку засыпного аппарата.
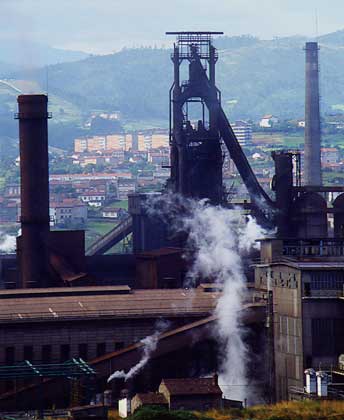
ДОМЕННАЯ ПЕЧЬ в Авилесе (Испания).
Эффективность доменной печи существенно повышается при использовании горячего дутья. Воздух, подводимый к фурмам, предварительно нагревается до температуры, которая может достигать 1000° C. Нагревание осуществляется в кауперах, каждый из которых ненамного уступает в размерах самой доменной печи. Каупер представляет собой вертикальный цилиндрический стальной кожух с внутренней "шахматной" насадкой из огнеупорного кирпича. Газ, отводимый с верхнего конца доменной печи, содержит моноксид углерода и другие газы, способные гореть. Этот газ по широким наклонным газоходам подводится к нижней части каупера, где, пройдя через пылевой фильтр, сжигается в камере горения. Продукты горения поднимаются вверх, нагревая кирпичную насадку. Когда насадка достаточно нагрета, перекрывают подачу топлива и газа в камеру горения и включают воздуходувки, которые гонят воздух через каупер в фурмы доменной печи. Для каждой доменной печи обычно предусматривают четыре каупера: два нагреваются, а два других подают горячее дутье. Потоки газа и воздуха периодически переключаются так, что непрерывно поддерживается заданная температура дутья. Существует ряд способов дополнительного повышения эффективности доменной печи. Один из них - работа при давлении внутренних газов, вдвое превышающем атмосферное. Это позволяет повысить производительность примерно на 15% и снизить потребление кокса примерно на 10%. Экономические преимущества повышения производительности в какой-то мере снижаются затратами на более мощное воздуходувное оборудование и возможным уменьшением срока службы огнеупорной кладки. При выпуске плавки из доменной печи шлак вытекает из своей летки, а металл - из своей, расположенной ниже. Ранее шлак заливали в шлаковозы - большие ковши на железнодорожных колесных тележках, которые доставляли незатвердевший шлак к отвалам. Теперь же шлак обычно отводят на перерабатывающую установку, расположенную рядом с домной, где он охлаждается водой и при этом гранулируется, после чего используется как заполнитель для бетона и пр.
Жидкий металл, вытекающий из летки, направлялся по желобам, подготовленным в песочной "постели" перед печью. Из желобов он растекался по удлиненным боковым углублениям в песке, где и затвердевал в виде болванок, называемых чушками (из-за сходства с многочисленными поросятами, сосущими свиноматку). Хотя литье в песок более не применяется, металл, выплавляемый в доменных печах, по-прежнему называют чушковым (применяется и термин "штыковой" чугун). В наши дни в тех случаях, когда требуется чушковый чугун, расплавленный металл разливают по стальным литейным формам, непрерывно движущимся перед домной на ленточном конвейере. Когда металл затвердевает, формы переворачиваются и, освободившись от чушки, возвращаются за следующей отливкой. Чтобы чугун не приставал к формам, их покрывают каменноугольной смолой или известью.
Чугун. Выплавляемый в доменной печи сплав железа с углеродом и кремнием имеет температуру плавления ок. 1150° C. В расплавленном состоянии чугун легко заполняет литейные формы любой конфигурации. Поэтому он очень подходит для изготовления многих видов изделий. Основные средства производства на чугунолитейном заводе - это плавильная печь, модели изделий и формовочные материалы. Из плавильных печей проще всего вагранка, т.е. небольшая печь шахтного типа, футерованная огнеупорным кирпичом. В ее нижней части имеются фурмы, а в верхней - дымоход для отходящих газов. Через боковое отверстие загружают топливо и чугун, печь разжигают и включают дутье. Расплавленный чугун собирается на подовой плите и по мере надобности выпускается через летку. На более крупных чугунолитейных заводах чугун плавят в отражательных печах. Для получения отливок хорошего качества нет необходимости в очень сложном оборудовании. Первый шаг - изготовление модели изделия. Модель изготовляет из дерева опытный мастер-модельщик, давая припуск на усадку чугуна при затвердевании. Литейные формы для чугунных отливок делают из формовочной смеси (глины с песком), липкой, но пористой. Модель помещают внутрь разъемной рамы, состоящей из "опок", и заполняют опоки формовочной смесью. Затем опоки разнимают и удаляют модель. Когда их снова складывают вместе, в формовочной смеси образуется полость литейной формы, точно соответствующая модели. Остается проделать литниковые отверстия и каналы, по которым жидкий чугун мог бы затечь в полость формы. После высыхания форма готова к заливке. Если заливка проходит хорошо, то жидкий чугун заполняет все пустоты формы, не оставляя воздушных пузырей. Когда чугун затвердевает, отливку "раздевают", разбивая форму. Во многих случаях для "доводки" изделия бывает достаточно сгладить шлифованием неровные края отливки. Чушковый чугун, чаще всего применяемый для литья, называют серым чугуном, поскольку серой, даже сажистой, выглядит его поверхность на изломе. Такой ее вид объясняется большим содержанием углерода (около 4%), присутствующего в железе в форме чешуек графита. Серый чугун жидкотекуч, имеет низкую температуру плавления и к тому же хорошо поглощает энергию вибрации - чугунный колокол не звенит. Благодаря этому чугун подходит для изготовления рояльных рам, станин прокатных станов, токарных, фрезерных и других станков. Очень распространенное изделие из серого чугуна - блок цилиндров автомобильного двигателя; чугун для этого применения хорош тем, что дешев и легко заливается в формы сложной конфигурации. Хотя серый чугун и прочен, он хрупок и легко разрушается при резком ударе. Поэтому вместо него чаще применяют ковкий чугун. Отливки из ковкого чугуна получают в два этапа. Сначала делается отливка из белого чугуна со сравнительно низким содержанием углерода и кремния. Такой чугун очень хрупок, но после высокотемпературного отжига в течение суток его пластичность намного увеличивается. Увеличение пластичности обусловлено перераспределением углерода в металле, происходящим при отжиге. В белом чугуне углерод содержится в форме карбида железа Fe3C. В процессе отжига карбид разлагается на железо и графит. Этот графит имеет вид малых сферических включений, которые, будучи отделены друг от друга, почти не снижают пластичность окружающей их железной матрицы. Из ковкого чугуна изготовляют трубопроводные фитинги и железнодорожное оборудование.
СТАЛЬ
Первоначально доменные печи строили в основном для выплавки литейного чугуна. Позднее были найдены способы переработки чугуна в сварочное железо, и металл доменной печи стал исходным материалом для такого железа. После разработки широкомасштабного и недорогостоящего производства стали на основе бессемеровского процесса и процесса Сименса стала экономически целесообразной переработка чугуна, выплавляемого в доменных печах, в сталь. В настоящее время почти весь чугун доменных печей идет на такой передел. Сталь - это особенно ценный конструкционный материал, которому можно придавать практически любую форму прокаткой, штампованием и прессованием, литьем или обработкой резанием. Путем легирования и термообработки можно получать стали с самыми разнообразными физическими и химическими свойствами. Так, например, одни стали настолько мягки, что их можно обрабатывать простым ручным слесарным инструментом, а другие столь тверды, что позволяют резать стекло.
ПРОЦЕССЫ ПРОИЗВОДСТВА СТАЛИ
При переделе в сталь чугуна, выплавленного в доменной печи, из него окислением удаляют почти весь углерод и весь кремний. Могут добавляться в качестве легирующих элементов марганец, никель или хром. В настоящее время основным способом переработки чугуна, выплавляемого в доменной печи, стал кислородно-конвертерный процесс, хотя кое-где еще применяется мартеновский процесс. Важной особенностью производства стали является относительная легкость ее повторного использования. И кислородный конвертер, и мартеновская печь могут работать с большим процентом стального металлолома (скрапа), а электропечь - и на одном скрапе. Это приобретает особенно важное значение в наши дни, когда обострилась проблема удаления отходов. Стоимость повторного использования в значительной мере зависит от качества металлолома. Металлолом, содержащий олово или медь, нежелателен в производстве стали, поскольку эти трудноудаляемые металлы ухудшают механические свойства стали. Наибольшую ценность представляет крупный металлолом, происхождение которого известно. Некоторые количества такого скрапа поступают с металлообрабатывающих заводов, а еще больше - после разборки устаревшего заводского и железнодорожного оборудования и разделки на металлолом морских и речных судов. Скрап в виде отработавших свой срок автомобилей и емкостей для продуктов питания менее ценен, так как он наверняка содержит медь и олово. Легирующие элементы обычно добавляют в сталь в виде ферросплавов. Ферросплавы содержат значительные количества железа, которое служит носителем легирующих элементов. К наиболее важным ферросплавам относятся ферромарганец (такой, как шпигель, или зеркальный чугун), необходимый для всех сталей; ферросилиций, применяемый для получения сталей со специальными магнитными свойствами и для раскисления сталей, выплавляемых в электропечах; феррохром и феррованадий. Никель добавляется в виде беспримесного металла.
Конвертерный процесс. В первой половине 20 в. первоначальный бессемеровский процесс постепенно утратил свое прежнее значение. Дело в том, что тепла, выделяющегося в бессемеровском конвертере, недостаточно для расплавления металлолома - более дешевого сырья, нежели горячий металл из доменной печи. Быстрое протекание плавки в бессемеровском конвертере не давало возможности провести анализы стали и скорректировать ее состав в соответствии со спецификациями. Мартеновский же процесс допускает значительный процент металлолома в загрузке печи, и реакции в нем протекают достаточно медленно, чтобы можно было успеть выполнить анализ в процессе плавки и провести коррекцию состава до выпуска металла.
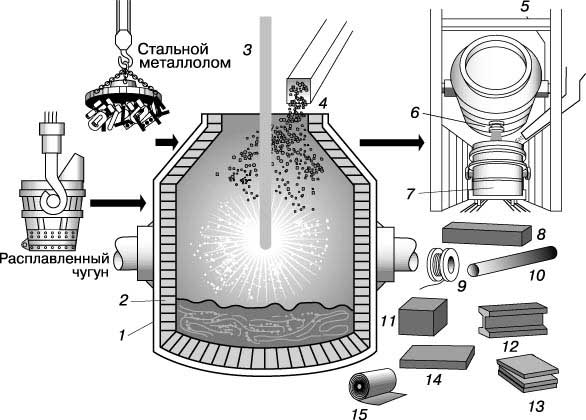
КИСЛОРОДНЫЙ КОНВЕРТЕР с верхней продувкой. 1 - стальной кожух; 2 - огнеупорная футеровка; 3 - кислородная фурма; 4 - завалка флюса; 5 - легирующие добавки; 6 - летка; 7 - ковш; 8 - заготовка; 9 - проволока; 10 - бесшовная труба; 11 - блюм; 12 - балка; 13 - толстолистовая сталь; 14 - листовая заготовка (сляб); 15 - листовой прокат.
Но в 1950-х годах конвертерный процесс производства стали снова вернулся к жизни и в течение следующих 35 лет полностью вытеснил мартеновский процесс, поскольку была разработана технология получения дешевого чистого кислорода, позволившая перейти с воздушного на кислородное дутье в конвертере. По этой технологии кислород в количествах, измеряемых тоннами, производят дробной (фракционной) перегонкой жидкого воздуха; для производства стали требуется кислород с чистотой 99,5%. Воздух - это на 80% азот, а азот - это инертный газ, не участвующий в реакциях конвертерной выплавки стали. Таким образом, в бессемеровском конвертере через расплавленный металл продувается большое количество бесполезного газа. Но этого мало - часть азота растворяется в стали. Последующее выделение растворенного азота в форме нитридов может приводить к ее последеформационному старению - постепенному уменьшению пластичности, которое приводит к трудностям при обработке давлением. Такого рода трудности отпадают, если металл в конвертере продувать не воздухом, а чистым кислородом. Но простой переход с воздуха на кислород в бессемеровском конвертере недопустим, так как из-за сильного разогрева фурм конвертер быстро выйдет из строя. Эта проблема была решена так: кислородное дутье подводится к поверхности расплавленного чугуна по трубе с водяным охлаждением. В 1952 35-тонный конвертер такого типа был успешно запущен в австрийском городе Линце на заводе фирмы VOEST. Такая технология, названная процессом ЛД (аббревиатура от Линца и Р.Дюррера, инженера фирмы), позднее была развита в кислородно-конвертерный процесс. Быстрая реакция окисления в конвертерной шихте, характеризующейся малым отношением площади поверхности к объему, сводит к минимуму потери тепла и позволяет вводить в шихту до 40% металлолома. Кислородный конвертер может каждые 45 мин выдавать 200 т стали, что в 4 раза превышает производительность мартеновской печи. Кислородный конвертер с верхней продувкой представляет собой грушевидный сосуд (с открытой узкой верхней горловиной) диаметром ок. 6 м и высотой ок. 10 м, облицованный изнутри магнезиальным (основным) кирпичом. Эта футеровка выдерживает примерно 1500 плавок. Конвертер снабжен боковыми цапфами, закрепленными в опорных кольцах, что позволяет наклонять его. В вертикальном положении конвертера его горловина находится под вытяжным колпаком дымоотводящего камина. Боковое выпускное отверстие, имеющееся с одной стороны, позволяет отделить металл от шлака при сливе. В конвертерном цеху рядом с конвертером обычно имеется загрузочный пролет. Сюда транспортируется в большом ковше жидкий чугун из доменной печи, а в стальных бункерах накапливается металлолом для загрузки. Все это сырье переносится к конвертеру мостовым краном. По другую сторону от конвертера расположен разливочный пролет, где имеются приемный ковш для выплавленной стали и железнодорожные тележки для транспортировки его на разливочную площадку. Перед началом кислородно-конвертерного процесса конвертер наклоняют в сторону загрузочного пролета и через горловину засыпают металлолом. Затем в конвертер заливают жидкий металл из доменной печи, содержащий около 4,5% углерода и 1,5% кремния. Предварительно металл подвергается десульфуризации в ковше. Конвертер возвращают в вертикальное положение, сверху вводят охлаждаемую водой фурму и включают подачу кислорода. Углерод в чугуне окисляется до CO или CO2, а кремний - до диоксида SiO2. По "течке" (загрузочному лотку) добавляется известь для образования шлака с диоксидом кремния. Со шлаком выводится до 90 % кремния, содержащегося в чугуне. Содержание азота в готовой стали сильно понижается благодаря промывающему действию CO. Приблизительно через 25 мин дутье прекращается, конвертер немного наклоняют, отбирают пробу и анализируют ее. При необходимости в корректировке можно снова возвратить конвертер в вертикальное положение и ввести в горловину кислородную фурму. Если же состав и температура расплава соответствуют спецификациям, то конвертер наклоняют в сторону разливочного пролета и через выпускное отверстие сливают сталь.
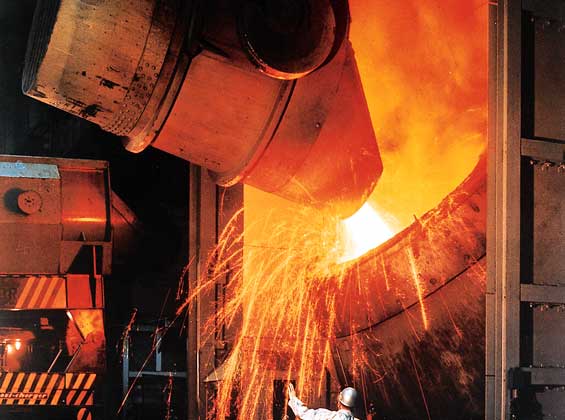
РАЗЛИВКА СТАЛИ (сталеплавильный завод в Бетлехеме, шт. Пенсильвания).
Кроме кислородно-конвертерного процесса с верхней продувкой, существует кислородно-конвертерный процесс с подачей кислорода в струе топлива через днище конвертера. Фурмы в днище конвертера защищаются одновременной продувкой природного газа. Такой процесс быстрее протекает, он более производителен, чем процесс с верхней продувкой, но менее эффективен в отношении расплавления металлолома. Однако нижнюю продувку можно сочетать с верхней.
Мартеновская печь. Как уже упоминалось, мартеновская выплавка стали еще применяется в ряде стран, хотя и постепенно заменяется кислородно-конвертерным процессом. Мартеновская печь обычно вмещает 500 т стали. Она имеет широкий неглубокий под и низкий арочный свод, отражающий тепло в сторону пода. Газ и воздух вводятся с одного конца и сгорают над подом. Чем ниже содержание углерода, тем выше температура плавления. Для достижения температуры, при которой плавится сталь с минимальным содержанием углерода, применяют принцип регенерации тепла. На обоих концах печи имеются регенерационные камеры с такой же кирпичной насадкой, как и в кауперах доменной печи. Продукты сгорания пропускаются через одну из этих камер. Когда футеровка достаточно нагрета, направление потоков через печь меняется на обратное. Поступающие воздух и газ воспринимают тепло от кирпичей насадки, а отходящие газы нагревают вторую камеру. Таким образом достигается экономия топлива и повышается рабочая температура. Мартеновская печь - крупное сооружение, и процесс выплавки стали занимает довольно много времени. На загрузку печи рудой, металлоломом и чугуном уходит ок. 5 ч, на расплавление - 4 ч и на рафинирование и корректировку окончательного состава стали - еще 3-4 ч. Чугун и металлолом могут загружаться в разных пропорциях в зависимости от потребности и экономических соображений. Термохимический процесс плавки стали в мартеновской печи сложен. Как уже упоминалось, главными примесями чушкового чугуна являются кремний Si, углерод C, сера S и фосфор P. Кремний реагирует с железной рудой [[оксидом железа (III) Fe2O3]], давая в результате диоксид кремния SiO2 и железо:

Углерод выгорает, образуя моноксид углерода CO и восстанавливая из руды железо:

Фосфор тоже, образуя пентоксид фосфора P2O5, высвобождает железо из руды:

Сера, реагируя с известью CaO и углеродом, образует сульфид кальция CaS и моноксид углерода CO:

Сульфид кальция и пентоксид фосфора переходят в шлак, плавающий на поверхности очищенного железа. Шлак представляет собой в основном силикат кальция CaSiO3, образующийся в реакции соединения диоксида кремния с известью:

В процессе плавки шлаку уделяется не меньше внимания, чем самой стали, так как хорошая сталь получается в результате реакций между шлаком и металлом.
Электрическая печь. Электропечи сначала применялись только для выплавки качественных инструментальных и нержавеющих сталей, выплавлявшихся до этого в тиглях. Но постепенно электропечи стали играть важную роль в производстве малоуглеродистой стали из металлолома в тех случаях, когда не требуется передела чугуна из доменной печи. В настоящее время ок. 30% нерафинированной стали выплавляется в электропечах. Наиболее распространены дуговые электропечи. Под дуговой сталеплавильной печи облицован огнеупорной кирпичной кладкой, свод охлаждается водой и может сдвигаться в сторону для загрузки печи. Через три отверстия в своде вводятся угольные электроды. Между электродами и металлоломом на поду печи зажигается дуговой разряд. В большой печи ток дуги может достигать 100 000 А. Плавка стали обычно производится следующим образом. Свод печи отводят в сторону, и на под печи осторожно загружают металлолом. После этого свод возвращают на место, а электроды опускают так, чтобы они на 2-3 см не доходили до верха загруженного металлолома. Зажигают дугу и по мере расплавления завалки постепенно увеличивают мощность. В печь вводят кислород для окисления углерода и кремния в завалке и известь для образования шлака. На этом этапе химия плавки такая же, как и в кислородно-конвертерном процессе. По окончании периода окисления отбирают пробу, анализируют ее и при необходимости корректируют состав. Затем выключают дугу, поднимают электроды, наклоняют печь и выпускают сталь в ковш. Электросталеплавильный процесс находит также важное применение в вакуумной плавке стали. Для этого обычно пользуются индукционными электропечами. Сталь помещают в графитовый тигель, окруженный медным змеевиком индуктора. На индуктор подается переменное напряжение высокой частоты. Вихревые токи, наводимые индуктором в графитовом тигле, нагревают его, поскольку удельное сопротивление графита довольно велико. Если тигель с индуктором помещен в вакуумную камеру, то сталь, плавясь в вакууме, освобождается от кислорода и других растворенных газов. В результате получается очень чистая сталь, не содержащая оксидов. Вакуумная плавка дорогостояща и применяется лишь в тех случаях, когда требуется особо прочная и надежная сталь, например для шасси самолетов. Улучшение механических свойств стали в результате вакуумной плавки связано с отсутствием частиц оксидов, на которых в обычной стали часто зарождаются трещины.
Литье стали. Заключительным этапом описанного выше процесса производства является литье стали в отдельные слитки или в непрерывный слиток. Для получения отдельных слитков сталь разливают по массивным чугунным изложницам. Как только сталь затвердевает, слитки отделяют от изложниц и еще горячими переносят в нагревательный колодец. Здесь большое количество слитков выдерживается при высокой температуре, пока они не будут готовы к прокатке. Разливка стали по изложницам, "раздевание" слитков (отделение от изложниц), их перемещение в нагревательный колодец и последующее извлечение