МЕТАЛЛОВЕДЕНИЕ ФИЗИЧЕСКОЕ - применение физических принципов и экспериментальных методов для изучения и целенаправленного улучшения характеристик металлов и сплавов. Среди экспериментальных методов, применяемых к металлам и сплавам, ведущим является микроскопия. Металлография, более старая дисциплина, занимающаяся микроскопическим исследованием сплавов на разных стадиях термической обработки, теперь составляет часть металловедения. Центральным понятием физического металловедения является понятие равновесия фаз в сплаве; его графическим выражением служат диаграммы равновесия, или фазовые диаграммы. Однако зачастую сплавы оказываются в неравновесных, "метастабильных" состояниях. Исследование перехода от метастабильного к устойчивому (равновесному) состоянию также является важной частью металловедения. Металлы и сплавы заполнены метастабильными дефектами, которые определяют их поведение под нагрузкой и при облучении. Интерпретация этого поведения образует третью составную часть металловедения.
ФАЗОВАЯ СТРУКТУРА МЕТАЛЛОВ И СПЛАВОВ
Металлы и сплавы являются, как правило, кристаллическими материалами, хотя обычно не имеют кристаллических граней, знакомых нам по минералам. Кристаллическая структура металлов и сплавов определяет их свойства, в частности анизотропию, т.е. неодинаковость свойств материала по разным направлениям в кристалле. Таким образом, свойства типа жесткости и теплового расширения для разных осей кристалла различны. Часто анизотропия металлического объекта незаметна, так как он состоит из мелких кристалликов (рис. 1), имеющих произвольную ориентацию кристаллических осей, что приводит к усреднению анизотропии в объекте как целом. Если, однако, кристаллические оси стремятся принять некоторое предпочтительное направление, то говорят, что объект имеет предпочтительную ориентацию, или текстуру.
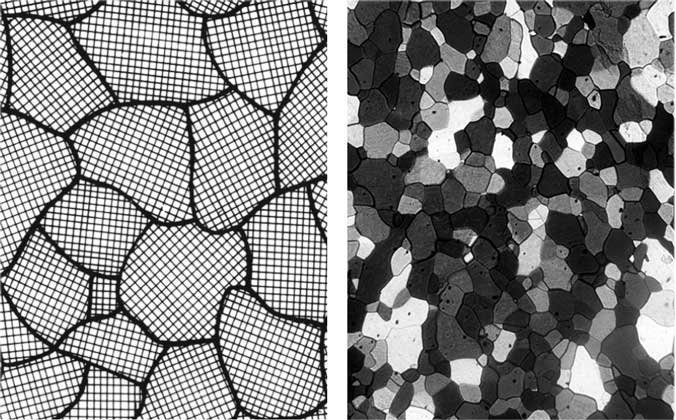
Рис.
1. КРИСТАЛЛИЧЕСКИЕ МАТЕРИАЛЫ обычно состоят из мелких зерен (слева). Поликристаллическая поверхность меди, рассматриваемая в поляризованном свете через оптический микроскоп, выглядит подобно лоскутному одеялу (справа).
Структура кристаллической решетки. Большинство простых металлов кристаллизуется в довольно простую структуру, например кубическую или гексагональную с плотной упаковкой, или в объемно-центрированную кубическую структуру, в которой атомы расположены в вершинах и центре кубической элементарной ячейки (рис. 2). Олово и уран могут служить примерами металлов, которые имеют более сложную кристаллическую структуру с тетрагональными или ромбическими элементарными ячейками.
См. также
КРИСТАЛЛЫ И КРИСТАЛЛОГРАФИЯ;
МИНЕРАЛЫ И МИНЕРАЛОГИЯ;
ФИЗИКА ТВЕРДОГО ТЕЛА.
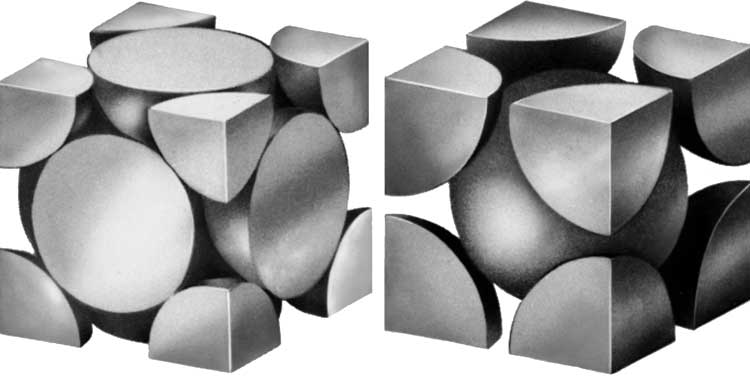
Рис. 2. ПРОСТЫЕ КРИСТАЛЛИЧЕСКИЕ СТРУКТУРЫ МЕТАЛЛА, демонстрирующие (слева) вид кубической гранецентрированной решетки, известной также под названием кубической решетки с плотной упаковкой, и (справа) вид объемно-центрированной кубической решетки.
Когда один металл хорошо перемешивается с другим, то образуется либо твердый раствор, либо интерметаллическое соединение. В твердом растворе атомы распределены произвольным образом и среднее расстояние между ними различно, но кристаллическая структура сохраняется. Интерметаллическое соединение обычно имеет кристаллическую структуру, которая отличается от структуры составляющих его металлов, а его атомы распределяются упорядоченным образом. Интерметаллические соединения в большинстве случаев имеют простую формулу, например CuZn, Ni3Al или Cu5Sn. Некоторые из них строго ограничены своим идеальным составом; для многих других, однако, характерен значительный диапазон возможных составов. В годы зарождения физического металловедения, когда еще не была ясна природа химической связи, интерметаллические соединения относили к дальтонидам и бертоллидам, названным так Н. С. Курнаковым в честь Дж. Дальтона (1766-1844), который отстаивал идею постоянной атомной основы химических соединений, и К. Бертолле (1748-1822), основателя учения об изменяющемся химическом равновесии. Теперь механизм соединения металлов стал более понятным, и указанные термины начинают выходить из употребления. Бертоллид неидеального состава представляет собой в действительности твердый раствор; твердый раствор, основанный на чистом металле, называют "предельным" ("граничным") твердым раствором.
Фазы. Сплавы могут содержать области из двух или более кристаллических структур, различающихся составом. В типичном случае одна область состоит из предельного твердого раствора и одна или несколько - из интерметаллических соединений. Такие области называются фазами. В частично расплавленном сплаве жидкая область также является отдельной фазой. Число, кристаллическая структура, состав и относительная доля фаз в сплаве, рассматриваемые как функции температуры и полного состава сплава, служат основой диаграмм равновесия. К их описанию мы и переходим.
ДИАГРАММЫ РАВНОВЕСИЯ
Представление об устойчивой комбинации фаз для материалов определенного состава при данных температуре и давлении восходит к американскому физику Дж. У. Гиббсу (1839-1903). Гиббс пришел к выводу, что, в принципе, даже химически чистый элемент может образовывать ряд различных кристаллических структур. Структура с самой низкой энергией образуется при равновесии. Понятие об этой энергии, получившей название энергии Гиббса (G), базируется на двух дополнительных понятиях - энтальпии и энтропии. Энтальпия H единицы массы металла может мыслиться как сумма энтальпий всех связей между соседними парами атомов этой массы. Энтальпия зависит от кристаллической структуры, потому что и число атомных пар, и расстояния между соседними атомами изменяются от структуры к структуре. (Принято считать, что самая прочно связанная совокупность атомов имеет самую низкую энтальпию.) Однако металл не обязательно будет образовывать структуру с самой низкой энтальпией при всех температурах. Это обусловлено тем, что тепловые колебания атомов влияют на прочность связи: чем выше температура, тем больше амплитуда колебаний и слабее связь. Величина этих колебаний выражается через энтропию S, которую удобно представлять как меру беспорядка. Энергия Гиббса G дается соотношением G = H - TS, где T есть абсолютная температура (измеряемая в градусах Кельвина). В твердом растворе (см. выше) энтропия зависит не только от тепловых колебаний атомов, но также от числа способов, которыми различные атомы могут быть распределены в кристаллической структуре. Это число характеризует беспорядок и увеличивается с ростом концентрации твердого раствора. Такой статистический аспект энтропии играет исключительно важную роль при определении равновесия системы сплава. Когда температура возрастает, материал становится существенно неупорядоченным. Близкая параллель может быть найдена в статистической энтропии эластичного полимера, которая является источником его сопротивления растяжению. Когда первоначально изогнутые полимерные цепи распрямляются, число возможных конфигураций уменьшается, и цепи теряют энтропию. Соотношение G = H - TS и вывод Гиббса о том, что самое низкое возможное значение G определяет, какая кристаллическая структура является устойчивой, обусловливают тот факт, что энтальпия и энтропия в физическом металловедении находятся в состоянии постоянной конкуренции. Диаграмма равновесия показывает, как рассчитывается эта конкуренция для двух и более металлов при разных их пропорциях и температурах. Рассмотрим диаграммы равновесия для некоторых систем сплавов, чтобы лучше уяснить изложенные принципы.
Система серебро - магний. Диаграмма равновесия для этой комбинации металлов показана в нижней части рис. 3. По вертикальной оси откладывается температура, а по горизонтальной - доля атомов магния в серебре. На диаграмме можно выделить пять однофазных областей: при высоких температурах, жидкость; при более низких температурах, область a, зона граничных твердых растворов, основанных на кубической кристаллической структуре серебра, характеризующейся плотной упаковкой; область g, основанная на гексагональной кристаллической структуре магния, характеризующейся плотной упаковкой; область b ў, (бертоллидное) интерметаллическое соединение AgMg с простой кубической структурой из атомов Ag в вершинах кубов и атомов Mg в их центрах; наконец, фаза e, более узкая бертоллидная область, соответствующая соединению AgMg3, структура которого имеет более сложную гексагональную элементарную ячейку. Эти однофазные области разделены двухфазными областями, в которых сосуществуют смежные фазы с составами, определяемыми границами с соседями, и изменяющиеся с температурой, причем относительные пропорции зависят от точки в пределах области, которая определяет температуру и общий состав. (Так, точка P определяет сплав с 0,6 долей атомов Mg, находящихся в равновесии при 600 К, т.е. 327° С.) Такой сплав иллюстрирует тот факт, что общий состав сплава совершенно отличен от состава равновесных фаз, если их две или более.
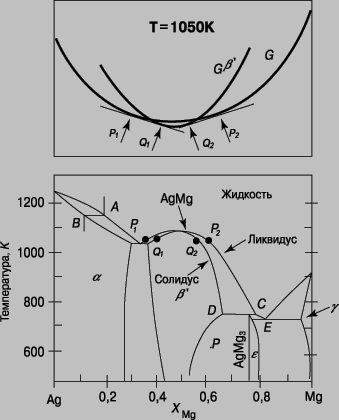
Рис. 3. ФАЗОВАЯ ДИАГРАММА СЕРЕБРО - МАГНИЙ.
Обычно расплав сплава не может затвердевать без изменения в составе. Поэтому, когда расплав состава A достигает линии ликвидуса, он начинает затвердевать в составе B, определяемом линией солидуса. Этот процесс изменяет состав остальной части расплава, обогащая его магнием, так что последующее затвердевание происходит при постепенно снижающихся температурах, образуя твердое тело непрерывно изменяющегося состава. Такой сплав имеет неравномерный состав, определяемый смещающимся равновесием в процессе его затвердевания. Если охлаждение происходит медленно, то миграция атомов в горячем твердом теле успевает выровнять состав сплава; при быстром охлаждении равновесие не успевает установиться. Это простой пример метастабильной структуры. Интерметаллическое соединение AgMg затвердевает "гармонично" - без изменения состава, т.е. можно сказать, что ликвидус и солидус при этом составе сплава совпадают; зачастую это служит для определения идеального состава бертоллида. Однако фаза e затвердевает в результате более сложного процесса, получившего название перитектической кристаллизации, которая включает взаимодействие между жидкостью состава C и твердым телом состава D. Наконец, в правой части диаграммы отражен процесс эвтектической кристаллизации. В этом случае сплав общего состава E застывает с образованием однородной двухфазной смеси фазы e и граничного твердого раствора, обогащенного магнием (так называемая эвтектическая смесь), а затем затвердевает при постоянной эвтектической температуре. Если сплав содержит немного больше или меньше Mg, чем сплав E, то одна или другая из упомянутых выше фаз затвердевает первой до тех пор, пока оставшийся расплав не достигнет состава E, после чего образуется эвтектическая смесь. Результат представляет собой двухфазную смесь, состоящую (в случае избытка магния) из областей крупных зерен твердого раствора, обогащенного магнием, с вкраплениями зон мелкозернистой эвтектической смеси, так что одна и та же фаза существует в двух различных микроструктурных формах. Верхняя часть диаграммы рис. 3 показывает оценку энергии Гиббса G при постоянной температуре 1050 К (777° С) с фазовым составом для жидкой и b ў фаз. Для данного общего состава сплава устойчивой фазовой структурой всегда является структура, соответствующая более низкому значению G, за исключением тех диапазонов состава, где общая касательная к двум кривым лежит ниже обеих кривых, например диапазоны P1Q1 и P2Q2. Здесь двухфазная смесь будет иметь более низкую энергию Гиббса, чем если бы сплав состоял исключительно из одной или другой фазы. Аналогичным образом могут быть интерпретированы все части диаграммы равновесия.
Система медь - золото. Эту систему часто относят к металлургической классике. На рис. 4 приведена часть диаграммы равновесия Cu - Au в упрощенном виде. Cu3Au представляет собой бертоллидное соединение, кристаллическая структура которого показана ниже (рис. 5,a). Когда это соединение претерпевает медленное нагревание в равновесном состоянии, оно при критической температуре TC = 390° С переходит в состояние, в котором атомы меди и золота распределены по узлам гранецентрированной кубической решетки произвольно. Это превращение называется переходом порядок - беспорядок. При дальнейшем нагревании неупорядоченная форма остается в равновесии до тех пор, пока не достигнет температуры плавления. Если соединение имеет нестехиометрический или неидеальный состав, например Cu78Au22, то TC снижается примерно до 350° С, и появляется узкая область, в которой упорядоченная и неупорядоченная формы соединения, слабо различающиеся составом, сосуществуют в равновесии.
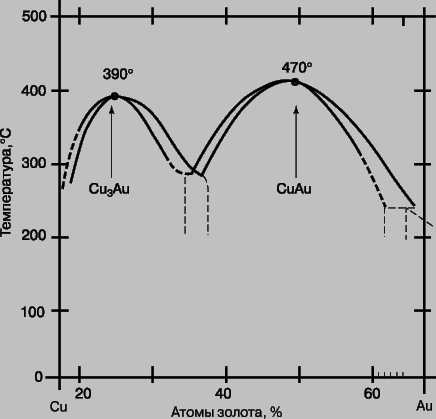
Рис. 4. ФАЗОВАЯ ДИАГРАММА МЕДЬ - ЗОЛОТО (фрагмент, упрощено).
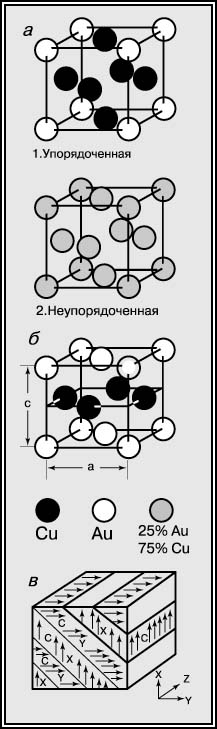
Рис. 5. КРИСТАЛЛИЧЕСКИЕ СТРУКТУРЫ Cu3Au (a) и CuAu (б). Схематическое изображение совокупности доменов CuAu, в которую превращается первоначально неупорядоченный одиночный кристалл (в).
Упорядоченная форма, например форма Cu3Au, существует потому, что имеет столько отличающихся друг от друга (Cu - Au) ближайших соседей в своей кристаллической структуре, сколько допускает эта формула. Такие соседи имеют сильные связи, заключающие в себе низкую общую энтальпию H. Переход порядок - беспорядок появляется потому, что TS в выражении G = H - TS увеличивается с ростом температуры до тех пор, пока для этого сплава не станет выгодным - в смысле энергии - беспорядок. В этом беспорядке возникает большое число однородных атомных пар (Cu - Cu и Au - Au), имеющих слабые связи, и H растет. Этот рост более чем компенсируется резким увеличением статистической энтропии, что обусловлено произвольным распределением атомов Cu и Au. Увеличение TS более чем компенсирует рост H, когда порядок в структуре уступает место беспорядку. Хорошей аналогией описанного поведения может служить эластичность резины. Когда резиновую ленту нагревают, ее сопротивление растяжению возрастает, потому что возрастает TS. Аналогичным феноменом является исчезновение ферромагнетизма при нагревании куска железа выше его температуры Кюри; отдельные атомные магнитики в железе ведут себя во многом так же, как атомные пары Cu и Au в Cu3Au.
См. также МАГНИТЫ И МАГНИТНЫЕ СВОЙСТВА ВЕЩЕСТВА. Для объяснения того, почему переход может быть резким (как в случае с Cu3Au), используются методы статистической физики - теории коллективного поведения больших совокупностей атомов. Когда достигается критическая температура, происходит нечто вроде схода лавины: чем больше атомов становятся неупорядоченными, тем легче остальные следуют за ними. Статистическая физика может придать смысл структурным переходам, предоставив информацию об относительной силе связей; однако она не может объяснить, почему связи Cu - Au прочнее связей Cu - Cu и Au - Au. Для этого необходимо применить квантовую механику. Как статистическая, так и квантовая теории имеют важное значение для исследований в современном физическом металловедении.
См. также КВАНТОВАЯ МЕХАНИКА; СТАТИСТИЧЕСКАЯ МЕХАНИКА. Если к рассматриваемому сплаву добавить больше золота, чтобы получить состав CuAu, наблюдается другой вид перехода порядок - беспорядок. Упорядоченная форма этого бертоллидного соединения показана на рис. 5,б. Упорядоченный CuAu имеет тетрагональную структуру, состоящую из последовательных слоев только Cu и только Au. Расчет показывает, что эта структура имеет больше отличающихся ближайших соседей, чем неупорядоченная (гранецентрированная кубическая) структура. Этот вид перехода порядок - беспорядок, связанный с изменением симметрии и размеров элементарной ячейки, приводит к интересным усложнениям. Указанная неупорядоченная форма имеет три равноценные оси куба, расположенные под прямыми углами друг к другу. Любая из этих осей может превращаться в тетрагональную ось c, так что одиночный неупорядоченный кристалл может превратиться в совокупность так называемых доменов, у каждого из которых есть некоторая ось c, по разному ориентированная относительно его непосредственных соседей; это схематически изображено на рис. 5,в. Поскольку ось с упорядоченного домена короче ребра куба, представляющего неупорядоченную элементарную ячейку, упорядочение вызывает локальные деформации в сплаве. Одним из следствий этого является то, что конфигурация доменов (рис. 5,в) оптимизируется таким образом, чтобы минимизировать суммарную энергию упругой деформации, так как различно ориентированные домены в какой-то степени уменьшают упругие деформации друг друга. Еще одно следствие состоит в том, что внешнее напряжение может изменять предпочтительную конфигурацию доменов, а в крайнем случае свести весь кристалл к одному домену. В современном физическом металловедении роль напряжения в определении структуры сильно возросла. Сплавы, близкие по составу к CuAu и содержащие малые количества других благородных металлов, используются для зубных коронок и мостов. При закалке с высокой температуры такой сплав становится метастабильно неупорядоченным и, в этом состоянии, мягким. При последующем нагревании до 200-300° С он упорядочивается и принимает сложную доменную структуру, которая гораздо тверже. Такая термообработка позволяет повысить прочность зубных коронок.
Система железо - углерод. Эта система имеет важное практическое значение в промышленности. Общепринятый вариант ее фазовой диаграммы приведен на рис. 6. Эта диаграмма, для которой характерна метастабильная фаза Fe3C (цементит), соответствует сталям. В чугунах, содержащих большое количество углерода, последний выступает в виде самой устойчивой фазы, т.е. в виде элементарного углерода (графита). В сталях углерод обычно не выделяется, и вместо него появляется цементит, образование которого идет легко. Таким образом, рис. 6 дает пример диаграммы метастабильной фазы.
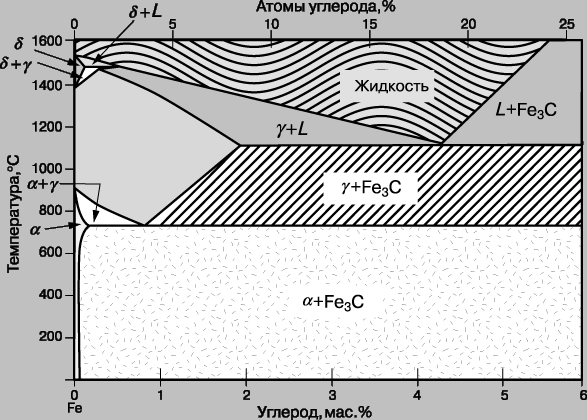
Рис. 6. ФАЗОВАЯ ДИАГРАММА ЖЕЛЕЗО - УГЛЕРОД (опущена графитовая фаза).
При термической обработке простых (т. е. железоуглеродистых) сталей существенным является то, что в зависимости от температуры они имеют две различные кристаллические структуры. При температурах немного ниже температуры затвердевания железо и растворы принимают структуру объемно-центрированной кубической решетки (дельта-фаза). При более низких температурах сталь превращается в аустенит (гамма-фаза) с гранецентрированной кубической решеткой. При еще более низких температурах происходит возврат к объемно-центрированной структуре, названной здесь альфа-фазой. (Переход от объемно-центрированной кубической решетки к гранецентрированной и обратно является уникальным для железа.) Понятие бета-железа исчезло из научного словаря, когда было осознано, что фаза, для описания которой оно предназначалось, не отражает никакого кристаллографического перехода. Фазы альфа и дельта также кристаллографически идентичны и имеют разные обозначения потому, что считались в прошлом двумя разными формами. Когда простая углеродистая сталь, содержащая 3,6 атомов углерода на 100 атомов сплава (3,6%), медленно охлаждается, в ней происходит эвтектоидная реакция. Эта реакция сродни эвтектической реакции (см. выше), но имеет место в твердом состоянии. Получающийся продукт представляет собой смесь, называемую перлитом и состоящую из почти чистого объемно-центрированного железа (называемого ферритом) и цементита. На рис. 7,а изображен полированный и травленный шлиф перлита, как он виден под микроскопом.

Рис. 7. МИКРОГРАФИЧЕСКИЕ ИЗОБРАЖЕНИЯ (полученные с помощью оптического микроскопа) перлита (а), мартенсита (б) и распределения частиц цементита в феррите (в).
Если, однако, подвергнуть аустенит закалке в воду, то перлит образоваться не успевает, а вместо него образуется структура, названная мартенситом. Это превращение не фигурирует на фазовой диаграмме, потому что мартенсит метастабилен по отношению к перлиту. На рис. 7,б представлено микрографическое изображение стали, которая была частично превращена в мартенсит. Мартенсит имеет искаженную форму объемно-центрированной кубической структуры, что делает его исключительно твердым и хрупким. При нагреве мартенсита до умеренной температуры он начинает превращаться в однородную смесь альфа-железа и цементита, становясь все более мягким и деформируемым. Это процесс отпуска - мартенситного старения. Например, высококачественному клинку или сабле придается нужная форма, когда сталь мягкая; при последующей закалке режущий край остывает очень быстро, а толстый медленнее. В результате режущая кромка становится очень твердой, а противоположный край - менее мартенситным и, следовательно, менее хрупким. Многие применяемые на практике стали представляют собой результат гораздо более сложной термической обработки, чем только что рассмотренная простая Fe - C сталь, и, кроме того, содержат другие легирующие элементы, такие, как хром, ванадий, ниобий и молибден. Эти присадки могут усиливать тенденцию образования мартенсита, благодаря чему и толстые детали допускают закалку. Каждая сталь характеризуется кривой зависимости превращения от времени и температуры (пример приведен на рис. 8), так что конструктор может получить путем термообработки любую желаемую структуру (и механические характеристики) выбранной стали.
См. также МЕТАЛЛОВ ТЕРМИЧЕСКАЯ ОБРАБОТКА.
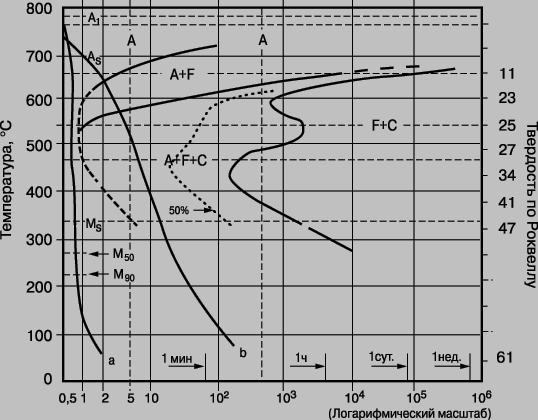
Рис. 8. КРИВЫЕ ЗАВИСИМОСТИ ВРЕМЯ - ТЕМПЕРАТУРА ДЛЯ ПРЕВРАЩЕНИЙ в стали, содержащей 0,4 мас. % углерода и 1,0 мас. % марганца. A - аустенит (гранецентрированная кубическая решетка); F - феррит (твердый раствор углерода в железе с объемно-центрированной кубической решеткой); C - цементит, Fe3C. MS - температура начала образования мартенсита при охлаждении; M90 показывает завершение процесса превращения на 90%. Кривая a соответствует закалке в воду и представляет только мартенсит; кривая b соответствует закалке в масло и представляет смесь мартенсита, феррита и цементита.
До недавнего времени катаный стальной лист, который используется для изготовления автомобильных кузовов, не мог быть подвергнут термообработке, поскольку огромные рулоны листовой стали слишком велики, чтобы можно было обеспечить быстрое и контролируемое изменение температуры. Теперь после отжига такой лист подвергают холодной прокатке и затем перед свертыванием в рулон пропускают через низкотемпературную печь и устройство контролируемого охлаждения. График температура - время выдерживается с помощью компьютерного управления каждой стадией процесса. В результате такой процедуры слабо легированный стальной лист может быть доведен до стандартов прочности, однородности и профиля, которые прежде были недостижимы. В результате автомобильный кузов стал легче и прочнее.
Тройные сплавы. Тройные системы имеют соответствующие фазовые диаграммы. Известным примером может служить система Ni - Al - Fe. Тройные фазовые диаграммы включают в себя трехфазные, двухфазные и однофазные области. Таким образом, это весьма сложные структуры, требующие трехмерного графического представления посредством призмы, в основании которой лежит равносторонний треугольник. Ось призмы представляет температуру, а каждая точка основания - конкретный тройной состав. Границы фаз изображаются двумерными сечениями. Четверные системы еще сложнее и редка становятся предметом исследования; они изображаются с помощью правильного тетраэдра, в котором каждая точка представляет конкретный состав (все такие точки относятся к одной температуре).
Расчет фазовых диаграмм. Время и усилия, затрачиваемые на расчет фазовых диаграмм, особенно тройных систем, было существенно сокращено благодаря разработке вычислительных методов типа CALPHAD. Термохимические величины, такие, как теплота образования и активность твердого раствора, могут быть измерены экспериментально и затем использованы для расчета расположения границ фаз. В частности, из измерений для трех двойных систем могут быть вычислены границы фаз в соответствующей тройной системе. Этот вид расчетов является весьма плодотворным в физическом металловедении.
ИНСТРУМЕНТАРИЙ ДЛЯ ИССЛЕДОВАНИЯ ХАРАКТЕРИСТИК СПЛАВОВ
До сих пор ничего не говорилось об экспериментальных методах, используемых для получения информации, о которой шла речь выше. Теперь мы обратимся к роли металлургических инструментальных средств в определении природы кристаллической структуры, положения фазовых границ в диаграммах равновесия, деталей перехода порядок - беспорядок и кинетики фазового превращения в легированных сталях при разных температурах. Для удобства методы исследования могут быть разделены на три категории: 1) средства определения кристаллической структуры, 2) средства наблюдения микроструктуры и 3) средства определения локальных изменений состава.
Рентгенография. В рентгенографии используются два метода. В порошковом методе совокупность мельчайших произвольно ориентированных кристаллических частиц облучается монохроматическим лучом. В методе монокристалла небольшой кристалл вращается, подвергаясь при этом облучению монохроматическим рентгеновским лучом, или же остается неподвижным, но облучается лучом, состоящим из волн разной длины; в любом случае, испытав дифракцию, лучи выходят в предпочтительных направлениях. Метод монокристалла используется для определения кристаллической структуры, а также для идентификации ориентации отдельных металлических кристаллов. Порошковый метод применяется для таких целей, как идентификация неизвестных соединений, определения границ фаз в фазовых диаграммах и изучения преимущественной ориентации кристаллических зерен в листах металла. Он применяется также для определения деформаций зерен поликристаллического металлического объекта, причем в качестве масштаба используются интервалы между плоскостями кристаллической решетки. Одним из более сложных приложений этого метода является измерение соотношения в пространственной ориентации между исходной фазой и фазой, образованной из нее при частичном превращении в процессе термообработки.
См. также РЕНТГЕНОВСКОЕ ИЗЛУЧЕНИЕ.
Микроскопия. Чтобы исследовать сплав под оптическим микроскопом, от него отделяют некоторую часть и механически или химически шлифуют ее, пока не получится очень тонкая пластинка, называемая шлифом. Затем этот шлиф травится в кислоте или другом реагенте так, чтобы можно было различить разные фазы. Чтобы изготовить шлиф оптимального вида, требуются большой опыт и мастерство. На рис. 7 приведены изображения микроструктур простой углеродистой стали. На рис. 7,а показан перлит, на рис. 7,б - структура мартенсита, а на рис. 7,в - мелкие фракции цементита в отпущенном мартенсите. Эти микрографические изображения хорошо иллюстрируют, что один и тот же сплав в результате той или иной термообработки может приобрести самые разные микроструктуры. Главное применение оптического микроскопа состоит в определении областей фаз в диаграммах равновесия. Сплав подвергается закалке с высокой температуры, затем изготавливается шлиф, который и изучается, чтобы идентифицировать фазы в микроструктуре. Эта идентификация может потребовать также использования других приборов, таких, как рентгеновский микроанализатор, описываемый ниже. За последние несколько десятилетий оптический микроскоп был дополнен двумя приборами, позволяющими различать гораздо более мелкие детали. Разрешающая способность оптического микроскопа ограничена длиной волны видимого света, так что детали, разделенные расстоянием менее 1 мкм, не поддаются разрешению. Просвечивающий электронный микроскоп может улучшить это разрешение в тысячи раз, позволяя различать детали, разделенные расстоянием примерно 0,2 нм. Получаемое изображение либо регистрируется на фотопластинке, либо проецируется на флуоресцентный экран. Растровый электронный микроскоп представляет собой разновидность электронного микроскопа и используется для исследования поверхности твердого тела.
См. также ЭЛЕКТРОННЫЙ МИКРОСКОП; МИКРОСКОП.
Определение локального состава. Сегодня специалисты в области физического металловедения располагают набором инструментов, которые могут не только производить автоматический анализ того или иного сплава, но также обнаруживать локальные различия в составе микроструктуры. Во всех таких инструментах для получения химической информации используются физические принципы. К указанным инструментам относятся масс-спектрометры вторичных ионов, рентгеновские фотоэлектронные спектрометры, оже-спектрометры и рентгеновские микроанализаторы. В упомянутом анализаторе электронный луч фокусируется на точке шлифа размером порядка 1 мкм. При этом можно получить информацию двух видов. Электроны, испытавшие обратное рассеяние, формируют изображение, как в растровом электронном микроскопе, позволяя различать разные фазы. Кроме того, благодаря торможению электронного луча сплавом происходит генерирование рентгеновских лучей с длинами волн, характерными для конкретного металла, присутствующего в сплаве. Эти длины волн измеряются. Электронный луч может сканировать исследуемую поверхность, а рентгеновские лучи, эмиттированные конкретной длиной волны электрона, могут быть поданы на электроннолучевую трубку, так что изображение поточечного изменения концентрации соответствующего металла может быть выведено на экран.
МИКРОСТРУКТУРА И СВОЙСТВА
Диаграмма равновесия определяет только составы, кристаллические структуры и объемные доли двух или более фаз, находящихся во взаимном равновесии. Форма, размеры и взаимное расположение областей, занятых разными фазами, не определяются уравнением Гиббса или диаграммой равновесия, связанной с этим уравнением. Исследование указанных переменных относится к исследованию микроструктур, которое представляет собой одну из четырех основных задач физического металловедения. Этими задачами являются: 1) исследование равновесия между фазами как функции состава и температуры, 2) исследование геометрии и преобразования микроструктур, 3) соотнесение полезных свойств, в частности механических, с присутствующими в сплаве фазами и их микроструктурным порядком и 4) скорость изменения микроструктуры и составляющих ее фаз в зависимости от температуры сплава и механизм этого изменения. Количественное исследование микроструктур требует измерения переменных величин, таких, как средний диаметр диспергированной фазы (например, иглы в эвтектике на рис. 9), отклонение фазы от сферической симметрии, среднее расстояние между элементами диспергированной фазы, объемные доли двух фаз, а также средняя длина свободного пробега - среднее расстояние, которое точка, движущаяся по прямой линии, проходит между последовательными встречами с диспергированной фазой. Все такие измерения должны быть подвергнуты статистической обработке, и должны быть определены среднее значение и дисперсия. Наука, занимающаяся извлечением этой информации из статистической выборки измерений на двумерных шлифах, называется количественной металлографией, или стереологией. Для формирования статистической совокупности измерений и получения численных результатов из исходных данных используются анализаторы изображений, оснащенные компьютерами. Поэтому анализатор изображения может быстро определить распределение средних диаметров кристаллических зерен, показанных на рис. 1, или средний интервал между пластинами цементита и их среднюю толщину в структуре перлита на рис. 7,а.
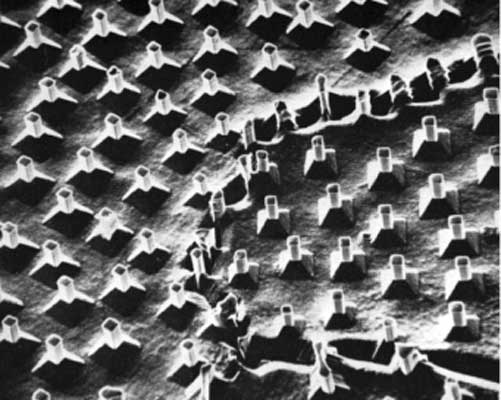
Рис. 9. ЭВТЕКТИЧЕСКАЯ МИКРОСТРУКТУРА, полученная направленным отвердеванием и состоящая из игл карбида тантала в никель-хромовой матрице. Изображение получено на растровом электронном микроскопе.
ЛИТЕРАТУРА
Физическое металловедение, в. 1-3. М., 1967-1968 Кауфман Л., Бернстейн Х. Расчет диаграмм состояния с помощью ЭВМ. М., 1972 Приборы и методы физического металловедения. М., 1973-1974 Кристиан Дж. Теория превращений в металлах и сплавах. М., 1978 Диаграммы фаз в сплавах. М., 1986